Choosing the Right Decorating Process
“Manufacturers decorate their products to differentiate them from those of their competitors. Often product designs are approved, marketing campaigns are launched, and expensive tooling is ordered without anyone ever confirming the design’s feasibility with regard to the decorating process that has been specified.
This blog will pair up some key design characteristics with the appropriate decorating process while identifying the benefits and limitations of one process versus another. Processes that will be discussed include pad printing, screen printing, hot stamping/heat transfer, in-mold decorating and piezoelectric DOD inkjet.
In researching this blog one of the first things I did was create a “Plastics Decorating Matrix” which I sent out to dozens of people within our industry; I chose both people that specialize in one process and people with experience in several processes. They were asked for their professional opinions in rating the processes mentioned for their suitability over a range of substrate materials, part and imaging characteristics, and sensitivity to conditions within the production environment.
While the responses were disappointingly limited, they confirmed what I know from 24 years of experience; very few plastics decorating applications have only one “right” solution. Each application is unique in some way, just as each process has benefits and limitations that play an integral role in determining whether or not it provides the “right” solution
Processes were rated on a scale of 1 to 4 (with the highest highlighted green in the table)
- 1 = Poor – process not suitable
- 2 = Fair – process is suitable with several limitations
- 3 = Good – process is suitable with minimal limitation
- 4 = Excellent – process is suitable without limitation
Compound Angles, Concave/Convex, and Spherical Parts
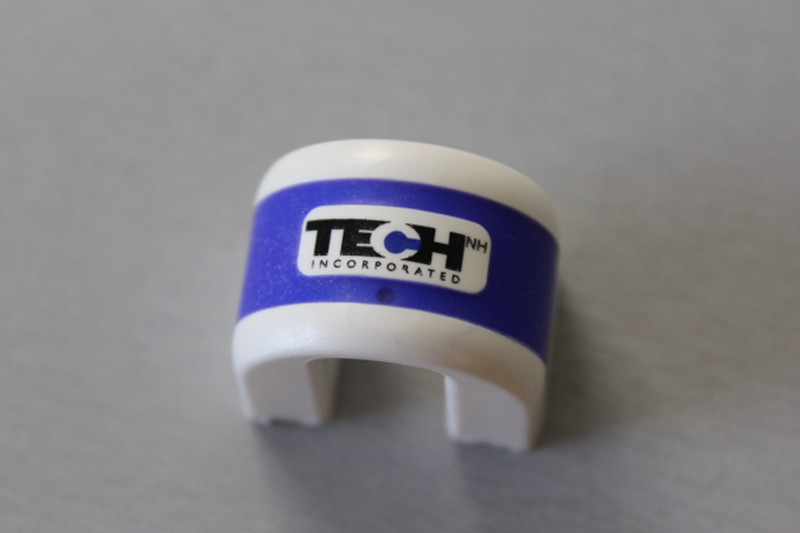
Pad printing has long been recognized as the process of choice for direct printing onto compound angles, concave and convex surfaces, and spherical objects. That is largely due to the transfer pad’s ability to pick up an image from a flat plane and conform to transfer it onto irregularly shaped surfaces with little or no distortion.
Alternatively, IMLs can provide a solution where run size requirements are larger and/or indirect decorating is preferred. IMLs, or pre=printed and/or pre-formed film inserts, are generally more expensive to produce, and may require that the artwork be pre-distorted. While IML enjoys (with exceptions) and advantage over pad printing for large image areas, it is generally not cost effective versus pad printing when the image only covers a small portion of the decorated surface.
Flat Parts, Raised, and Recessed Graphics
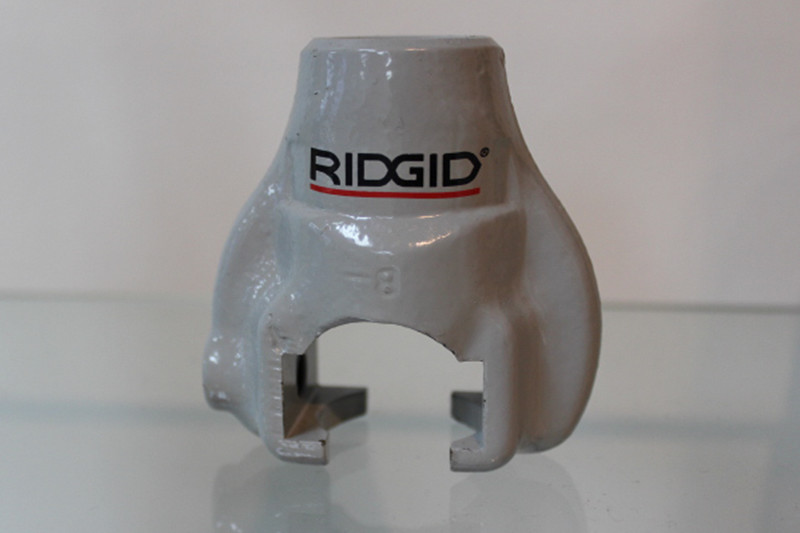
Screen printing and hot stamping/heat transfer are generally the “go-to” processes for use in decorating flat parts. Screen printing being the obvious choice for areas of large coverage, and hot stamping/heat transfer decorating is not affected by extremes or variations in temperature and relative humidity within the production environment.
Raised and recessed graphics are generally decorated via the vertical hot stamping process; unless there are surface irregularities in raised graphics, in which case a roll-on press is generally used.
IML applications work best on flat surfaces or on large radii. Long narrow images with pointed corners do not work very well because the force of the material flow in the mold tends to move the label out of position during molding.
Cylindrical Parts
Cylindrical items, such as 5 gallon paint pails, are typically screen printed. Rotary pad printing is also useful for smaller format parts such as syringe barrels and closures, and can reach extremely high speeds (400-600 parts per minute), even with U.V. curable inks.
Heat transfers may also be applied to cylindrical parts. For coverage of less than 85 degrees, a curved silicone rubber die can be made to fit the curve of the plastic part. For coverage up to 360 degrees, transfers can be applied by rolling the parts under and flat silicone die, with pre-registered transfers sandwiched in between on a web.
Hollow Parts
Hollow parts such as blow molded containers, are usually screen printed or labeled with pre-printed PSA (pressure sensitive adhesive) labels. For more rigid parts with smaller diameters and/or thicker sidewall constructions, hot stamping/heat transfer can be an alternative.
Pad printing is becoming more widely used when hollow parts have complex geometries that are too difficult or impossible to screen print, label, or dimensionally stable it is essential to inflate the parts equally, at each print station, to ensure registration of the image.
Textured Parts
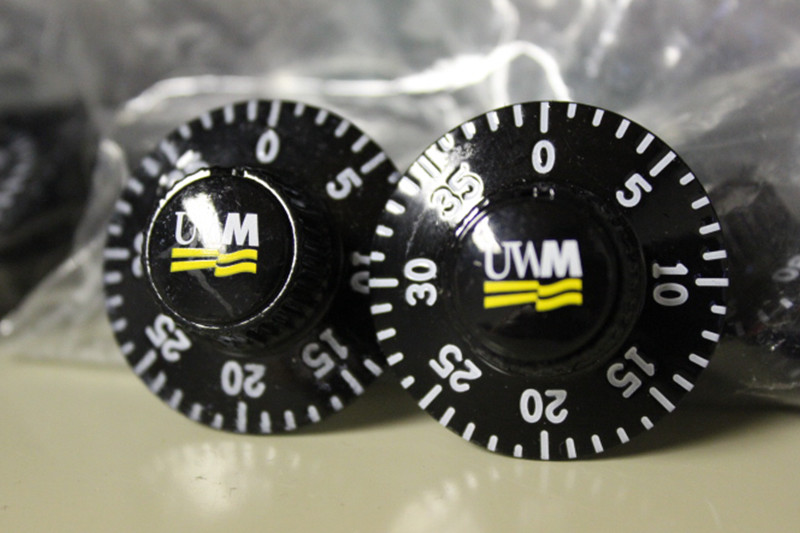
Textures are almost always a gamble. In an attempt to find a correlation between characteristics of different textures and printability, I pad printed a series of sixty-odd black “visual texture standard” plaques, provided by Mold-Tech. I used an automotive-approved, two-component, white ink-thinned (15 percent by weight), a steel cliche (etch depth of 23 microns) and a 9-shore (scaled c) transfer pad with a high angle.
Each plaque was single-printed at one end and double printed on the other, then allowed to dry per the ink manufacturer’s recommendation. The plaques were then visually inspected for coverage under a uniform, non-directional (unfocused) light source at a distance of 18″ for approximately ten seconds (per Ford Motor Company visual inspection procedure for automotive interior parts). Acceptance or non-acceptance was determined by the presence of any visible defect or void resulting from insufficient coverage of the texture.
The results indicate that the frequency of the texture plays a significantly larger role in achieving an acceptable print than the depth of the texture or the angle of the sidewalls. One texture having a depth of .0055″ and 8 degrees draft couldn’t be printed successfully at all. The difference was the number of peaks and valleys in the texture within the image area. The obvious conclusion: the higher the frequency, the lower the likelihood of acceptance.
Textures can be compensated for, however, by depositing more ink. That makes screen printing a great solution for flat or cylindrical parts. For large image areas and/or complex geometries, your only choice may be to apply IMl technology
Image characteristics are a little harder to quantify than part characteristics, mostly due to the fact that many applications are comprised of a wide variety of different kinds of graphics; bold and finely detailed, metallic and matte, etc.
Wet-on-wet/Personalization/Serializing
Piezoelectric DOD inkjet is the only process in the survey that received an “excellent”, and it was for wet-on-wet. For short run CMYK and personalizing or serializing, you would have a hard time finding a better solution. with today’s U.V. inkjet formulations, more and more specialty advertising, small format signage, and promotional marketing applications are going with DOD inkjet.
Multiple Color and Fine Detail
New generation YAG lasers, laser cliche materials, and digitally controlled, multiple-axis pad printing systems in printers are producing lines only microns in width, and CMYK images with 1200 d.p.i. resolution, even on complex geometries. Screen printing provides nearly equivalent quality, as does IML.
Heat transfers are a viable alternative for those that don’t wish to become printers. Transfers are generally manufactured using one of three processes: screen printing, rotogravure, or flexographic. Screen is very similar in that it allow for brilliant colors. rotogravure provides superior resolution but is more attune to larger quantities due to the increased setup time. Flexography is least expensive but does not provide the brilliance of screen printing or the resolution of rotogravure.
Metallic Finish
Hot stamping continues to be the process of choice for high gloss, metallic finishes like those found on cosmetics. In fact, hot stamping is the only process where the bright gold and silver metallic finishes found on cosmetic packaging can be produced. IML is generally not recommended for applications requiring foils or metallic inks because they will not adequately maintain a static charge (required to stay in location within the mold) and because they can arc to the mold surface, causing pitting.”
John Kaverman is the technology coordinator for Innovative Marking Systems of Lowell, MA. He holds a degree in printing from Ferris State University and has over 20 years of combined screen and pad printing experience. He may be reached at john@padprinters.com